Manual, Semi-Automatic, or Fully Automatic Strapping Machines: Understanding the Differences
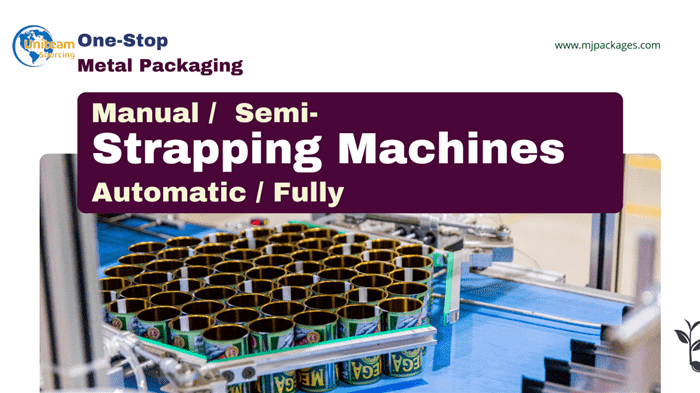
Strapping machines are indispensable tools in the packaging industry, designed to secure products for transport or storage. However, with a variety of options available, businesses often face the challenge of choosing the right type of strapping machine. From manual strapping machines to semi-automatic strapping machines, and fully automatic strapping machines, understanding the differences is crucial. In this article, we’ll break down the features, benefits, and applications of these machines while also looking at essential components like high-speed strapping, adjustable tension, and eco-friendly strapping materials.
Manual Strapping Machines
Manual strapping machines are the simplest and most cost-effective solution for smaller operations. These machines require an operator to feed the strap around the product, apply tension, and seal the strap by hand. While manual strapping machines are ideal for low-volume tasks, they are labor-intensive and slow compared to their more automated counterparts.
Key Features:
- Labor-Intensive: Requires manual intervention throughout the strapping process.
- Affordable: One of the most cost-effective options available, particularly for small businesses or occasional use.
- Flexible: Can handle a variety of products and strap types like polyester strapping, polypropylene strapping, or steel strapping.
Pros:
- Simple and inexpensive to purchase and maintain.
- Perfect for small businesses with low-volume strapping needs.
- Can accommodate different strapping materials, making it versatile for various packaging requirements.
Cons:
- Slow throughput, leading to higher labor costs.
- Potential for inconsistent tension and improper seals due to human error.
- Labor-intensive, requiring more staff to maintain production levels.
While manual strapping machines still have their place in many small-scale operations, they are increasingly being replaced by more efficient, automated systems in larger businesses.
Semi-Automatic Strapping Machines
A step up from manual machines, semi-automatic strapping machines require less operator involvement. With these systems, the operator manually places the product in the machine, and the machine automatically feeds, tensions, and seals the strap. Semi-automatic strapping machines are designed to reduce manual labor while still offering flexibility and affordability.
Key Features:
- Automatic Strapping: Reduces human involvement in the strapping process, improving efficiency and consistency.
- Adjustable Tension: Most semi-automatic systems offer adjustable tension control, which allows you to modify the tightness of the strap based on the product being strapped.
- Versatile Material Compatibility: Can be used with a wide range of strapping materials, including polypropylene strapping, steel strapping, and eco-friendly strapping options.
Pros:
- Faster than manual systems, significantly improving throughput.
- More consistent results with less human error.
- Still relatively affordable, providing a balance between automation and cost.
- Suitable for medium-volume packaging and companies that require flexibility with various strapping materials.
Cons:
- Requires some manual intervention, particularly with product placement.
- Not ideal for very high-volume operations or high-speed production lines.
- Still requires operator training and routine maintenance.
Semi-automatic strapping machines are popular in industries such as retail packaging and logistics, where medium-to-high volume strapping is required, but full automation is not yet necessary.
Fully Automatic Strapping Machines
For businesses with high-volume needs, fully automatic strapping machines offer the most efficient and hands-off solution. These machines, such as Uniteam Sourcing's Fully Automatic PE Tape High-Speed Empty Can Strapping Machine (Model: BKM-500), automate the entire strapping process—from feeding the strap to adjusting tension and sealing, all without operator intervention.
Key Features:
- High-Speed Strapping: Machines like the BKM-500 can strap up to 500 cans per minute, making them ideal for industries that require rapid throughput, such as food canning or e-commerce packaging.
- Automatic Control Systems: With features like servo-controlled strapping machines and fault self-diagnosis, these machines ensure precision and reliability.
- Eco-Friendly Strapping: Fully automatic machines can use food-grade PE tape that meets food safety standards and is recyclable, reducing waste and promoting sustainability.
Pros:
- Maximum Efficiency: Fully automated machines provide the highest throughput and eliminate human error.
- Reduced Labor Costs: The automation of the strapping process allows businesses to save on labor costs and reduce worker fatigue.
- Consistency and Precision: With features like tension control, adjustable tension, and interlocking control systems, these machines guarantee precise and uniform strapping every time.
- Environmentally Friendly: Fully automatic machines can use biodegradable strapping and eco-friendly materials, aligning with sustainability goals.
Cons:
- High Initial Investment: These machines come with a higher price tag, making them suitable for larger businesses or those with high-volume needs.
- Space Requirements: Due to their size and complexity, these machines often require more space in a production line.
- Specialized Maintenance: More advanced machines may require expert maintenance and operator training.
Uniteam Sourcing's BKM-500, for example, is equipped with an advanced control system, which integrates seamlessly with other packaging processes, ensuring that each can is strapped with precision and care. The servo-controlled strapping system enhances flexibility and allows easy adjustment for different product specifications.
Which Strapping Machine is Right for Your Business?
Choosing between a manual strapping machine, a semi-automatic strapping machine, or a fully automatic strapping machine depends on your production needs, budget, and the types of products you are packaging.
- Manual strapping machines are ideal for small-scale operations with low volume and diverse packaging needs. They are inexpensive but labor-intensive.
- Semi-automatic strapping machines are a good choice for medium-volume businesses seeking to improve speed and consistency without a major investment. They strike a balance between automation and cost-efficiency.
- Fully automatic strapping machines like the BKM-500 from Uniteam Sourcing are the best choice for high-volume industries that need maximum speed, efficiency, and minimal labor. These systems also offer advanced features like adjustable tension, tension control, fault self-diagnosis, and eco-friendly strapping options, making them ideal for modern, sustainable packaging operations.
Conclusion
The decision to invest in a manual, semi-automatic, or fully automatic strapping machine should be based on your business’s specific packaging needs. While manual strapping machines offer simplicity and low cost, semi-automatic and fully automatic strapping machines offer improved efficiency, speed, and precision. Fully automatic systems, such as the BKM-500, provide high-speed strapping with minimal labor, making them a top choice for high-volume industries like food packaging and logistics.
As the packaging industry continues to evolve, embracing advanced technologies in strapping equipment can lead to significant improvements in productivity, cost savings, and sustainability.
Need expert advice on strapping solutions? Contact Uniteam Sourcing today for personalized recommendations on the best strapping machines for your business needs.
News Recommended
Easy open lids are transforming canned food packaging by offering unparalleled convenience, safety, and sustainability. Consumers prefer these lids for their effortless opening experience, while manufacturers benefit from improved food safety and brand loyalty. Made from recyclable materials like tinplate and aluminum, easy open lids contribute to sustainability efforts by reducing waste and lowering carbon footprints. From canned foods to beverages, the demand for easy open lids continues to grow, shaping the future of packaging innovation. This article explores their benefits, industry impact, and emerging trends in packaging technology.
The canning industry faces increasing pressure to enhance efficiency, reduce operational costs, and maintain packaging consistency. Advanced packaging machinery, such as automated strapping and palletizing systems, offers a solution by minimizing manual labor bottlenecks and improving productivity. Uniteam Sourcing provides cutting-edge packaging solutions tailored to the needs of canning factories, helping businesses scale production, reduce product damage, and secure reliable distribution. Learn how integrating automation into your operations can enhance efficiency, ensure product safety, and give you a competitive advantage in the global market.
Selecting the right food packaging material is crucial for product safety, shelf life, and sustainability. Tinplate cans provide strong durability, excellent food preservation, and high recyclability, making them a preferred choice for many manufacturers. Aluminum cans and plastic containers offer alternative benefits, such as lightweight portability and cost efficiency, but have different environmental and functional trade-offs. This article explores the strengths and weaknesses of each packaging type, offering insights for businesses looking for bulk packaging solutions, contract manufacturing, and global distribution strategies.
Products