Troubleshooting Common Issues in Pail Can Automatic Strapping Machines
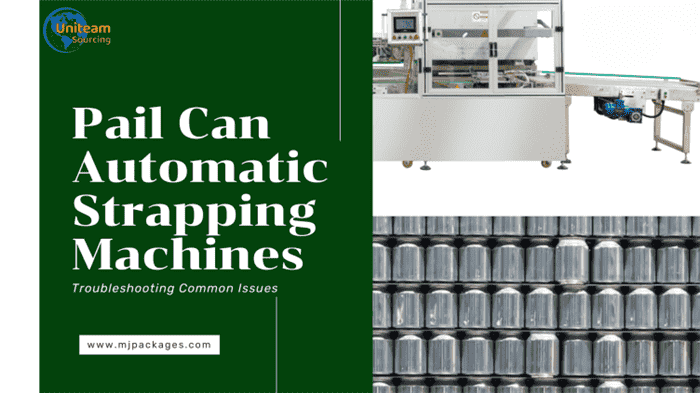
Pail can automatic strapping machines play a critical role in the packaging industry, particularly for businesses requiring fast, reliable, and efficient packaging solutions for pail containers. These machines are designed to secure containers by applying a strap, which is essential for protecting products during transportation and storage. However, like any industrial machinery, pail can automatic strapping machines can encounter issues that can cause disruptions in the production process.
1. Misalignment and Jamming
Misalignment and jamming are among the most frequent problems experienced in pail can automatic strapping machines. These issues can halt production and lead to costly delays.
Causes of Misalignment and Jamming:
- Incorrect Pail Placement: If the pail can is not properly positioned in the machine, it can result in misalignment and prevent the strap from feeding through the machine correctly.
- Worn or Misaligned Guide Rollers: The guide rollers direct the strap and are crucial to its smooth operation. Over time, they can become worn or misaligned, causing the strap to veer off course and leading to jams.
- Faulty or Dirty Sensors: The sensors in the machine help to detect the position of the pail can and the alignment of the strap. When these sensors become dirty or malfunction, the machine may fail to detect proper alignment, resulting in jamming.
- Incorrect Strap Tension: The tension of the strap plays a crucial role in its ability to be applied correctly. If the tension is too high or too low, the machine may encounter issues feeding or securing the strap.
Solutions for Misalignment and Jamming:
- Ensure Proper Pail Placement: Before starting the machine, double-check that the pail cans are correctly centered and aligned with the machine. This will prevent misalignment during the strapping process.
- Inspect and Align Guide Rollers: Regularly inspect the guide rollers for wear and tear. Replacing or adjusting them will help keep the strap feeding properly and reduce misalignment.
- Clean or Replace Sensors: If the sensors are malfunctioning, cleaning or replacing them will restore the machine’s ability to detect the position of the pail and the strap alignment, reducing jamming.
- Adjust Strap Tension: Fine-tune the strap tension settings to ensure that the strap is applied correctly without causing jams or excessive tightness.
2. Strap Feeding Problems
Strap feeding is critical to the proper functioning of pail can automatic strapping machines. Any issues in the strap feeding mechanism can delay or halt production entirely.
Causes of Strap Feeding Problems:
- Low or Empty Strap Supply: If the spool of strapping material is empty or nearly empty, the machine will not be able to feed new material through the system.
- Strap Tangles or Kinks: Improperly stored or handled strapping material can become tangled or kinked, preventing it from feeding smoothly into the machine.
- Damaged Feed Mechanism or Rollers: The feed rollers are responsible for guiding the strap from the spool to the pail can. Over time, they can become worn or damaged, causing feeding issues.
- Incompatible Strap Material or Width: If the strap material used is not the correct width or type for the machine, it may not feed correctly.
Solutions for Strap Feeding Problems:
- Refill Strap Supply: Ensure the strap supply is adequate before beginning production. Regularly monitor strap levels and replace the reel when it’s nearly empty.
- Untangle and Rewind Strap Material: Inspect the strap for kinks or tangles before feeding it into the machine. Proper storage of strapping material can also help prevent tangling.
- Check Feed Mechanism: Regularly inspect the feed rollers for wear. If needed, replace them to keep the strap feeding smoothly.
- Verify Strap Compatibility: Ensure that the strapping material and strap width are compatible with your machine. Consult the manufacturer’s recommendations for optimal strap specifications.
3. Malfunctioning Strapping Tools
The strapping tools in pail can automatic strapping machines are essential for tensioning and sealing the strap. Malfunctioning tools can result in poor-quality strapping, compromising the stability and protection of the packaged products.
Causes of Malfunctioning Strapping Tools:
- Worn or Broken Tensioning Mechanism: If the tensioning mechanism becomes worn or broken, it may not apply the proper tension to the strap, leading to loose or poorly secured strapping.
- Faulty Sealing Mechanism: The sealing tool bonds the strap together after it is tensioned. If it’s malfunctioning, the strap may come loose during handling, leading to packaging failure.
- Overheated or Clogged Heat Sealer: Many automatic strapping systems use heat sealing. If the heat sealer is clogged or overheated, it may fail to bond the strap properly, leading to weak or broken seals.
- Incorrect Strap Alignment: If the strap is not aligned correctly during the application process, it may result in an improperly sealed or tensioned strap.
Solutions for Malfunctioning Strapping Tools:
- Inspect the Tensioning Mechanism: If you notice inconsistencies in the tensioning of the strap, inspect the mechanism for wear. Replace or adjust the tensioning components as necessary.
- Clean and Maintain Sealing Tools: Regularly clean and calibrate the sealing tools to ensure proper bonding. If necessary, replace the sealing components to maintain the integrity of the strapping.
- Check Heat Sealer Functionality: If the machine uses a heat sealing system, check that the temperature settings are correct. Clean the heat sealer to prevent overheating or clogs.
- Align the Strap Properly: Ensure that the strap is aligned correctly before the strapping process begins. Misalignment can cause weak seals and improper tension.
Uniteam Sourcing's Advanced Solution: BFM-Y50 ARR Strapping Machine
At Uniteam Sourcing, we are proud to offer the cutting-edge BFM-Y50 ARR automatic strapping machine, which stands as a benchmark for excellence in the pail can strapping industry. Our machine is the result of independent research and development, and it has pioneered technological advancements both domestically and internationally. The BFM-Y50 ARR is designed to fill the technological gap in the metal packaging industry, offering a smarter solution for high-speed strapping.
This machine is primarily used for high-speed PE belt strapping of empty food cans, with a maximum speed of 500 cans per minute, making it ideal for high-volume production environments. Here are some key specifications and features of the BFM-Y50 ARR:
- Max Strapping Capacity: 8 bundles per minute, which can save 1-3 laborers by eliminating the need for manual strapping or stacking.
- Strapping Material: 12mm * 0.63 PE belt, offering reduced costs compared to semi-automatic machines.
- Adjustable Knot Height: Easily adjustable through the touch screen, ensuring versatility for different can types.
- Self-Diagnosis and Alarm System: Built-in fault self-diagnosis and alarm features to alert users in case of malfunctions, reducing downtime.
- Productivity Enhancement: The machine helps maintain the appearance of the cans by avoiding manual contact, which prevents rusting and maintains the product quality over time.
- Energy Efficiency: The BFM-Y50 ARR operates at a high level of energy efficiency, with a low-cost operation compared to traditional manual strapping solutions.
With features designed for higher efficiency, Uniteam Sourcing's BFM-Y50 ARR is the perfect solution for industries looking to automate their packaging processes and reduce labor intensity while improving production rates.
For more information about the BFM-Y50 ARR or any of our pail can strapping machines, feel free to reach out to us at Uniteam Sourcing, where innovation meets reliability in the packaging industry.
News Recommended
Electrolytic tinplate is a top-tier material for high-quality food can packaging, offering unmatched durability, food safety, and sustainability. Its corrosion-resistant properties and airtight sealing capabilities help preserve food freshness for extended periods. Tinplate cans provide better protection than aluminum and plastic alternatives, making them ideal for canned foods, beverages, and pet food. With its recyclability and compliance with global food safety standards, tinplate is a preferred choice for manufacturers seeking reliable and eco-friendly packaging solutions. Explore the benefits and applications of tinplate in modern food packaging.
Strapping machines are essential for securing products in transport and storage, but choosing the right type—manual, semi-automatic, or fully automatic—depends on your business needs. Manual strapping machines offer cost-effective solutions for low-volume tasks, while semi-automatic models balance automation and affordability. Fully automatic strapping machines, such as high-speed PE tape strapping systems, maximize efficiency, minimize labor costs, and support eco-friendly packaging. This guide explores the advantages, key features, and best applications of each type to help businesses optimize their packaging operations.
Easy open lids are transforming canned food packaging by offering unparalleled convenience, safety, and sustainability. Consumers prefer these lids for their effortless opening experience, while manufacturers benefit from improved food safety and brand loyalty. Made from recyclable materials like tinplate and aluminum, easy open lids contribute to sustainability efforts by reducing waste and lowering carbon footprints. From canned foods to beverages, the demand for easy open lids continues to grow, shaping the future of packaging innovation. This article explores their benefits, industry impact, and emerging trends in packaging technology.
The canning industry faces increasing pressure to enhance efficiency, reduce operational costs, and maintain packaging consistency. Advanced packaging machinery, such as automated strapping and palletizing systems, offers a solution by minimizing manual labor bottlenecks and improving productivity. Uniteam Sourcing provides cutting-edge packaging solutions tailored to the needs of canning factories, helping businesses scale production, reduce product damage, and secure reliable distribution. Learn how integrating automation into your operations can enhance efficiency, ensure product safety, and give you a competitive advantage in the global market.
Products